Components and dies for the food sector
The Food Industry has specific requirements that are met by selecting the appropriate materials and product manufacturing methods, including stamping.
Materials
The materials used in the food industry must guarantee that there is no molecule migration from the material into the food. From a technical point of view, the ideal material for this type of application is stainless steel. In particular, the AISI 318 variety guarantees excellent impermeability to acids and bases. Many products are therefore manufactured using this type of material. Another stainless steel variety in the industry is AISI 316. Obviously, for deep drawing, it is particularly important to use the versions that are specially developed for these processes.
Italian Decree No. 72 of 9 May 2019 states what types of stainless steel can be used in contact with food in Italy.
https://www.gazzettaufficiale.it
Another commonly used material is aluminium. In this case, there are some limitations related to the types of material that can be in contact with aluminium and to the temperature of food when in contact with the material. There are several different applications. Stainless Steel is normally used in applications where the food is in direct contact with the material and when particularly aggressive chemical agents may be used for cleaning and sanitising/sterilising the components, while Aluminium is preferred when the component needs to be lighter in weight, or when an optimised heat exchange between the component and the food is needed (thanks to the thermal conductivity of about 200W/mK of 1050 pure aluminium compared to 15W/mK of AISI 318 steel).
Over time, F.lli Poli have been increasingly adapting their production capacity to the processing of different materials.
Food and/or beverage containers, as well as any machinery that come into contact with food (dishwashers, ovens, and the like), food packaging machines, and sterilising equipment are all normally made of stainless steel.
One of the reasons is that they are easier to clean, as very aggressive agents can be used without any damage to the surface.
Food cold treatment trays, on the other hand, are preferably made in aluminium, which can keep its mechanical characteristics even at very low temperatures.
The general requirements that all food contact materials must meet are regulated by the Framework Regulation EC 1935/2004.
FCM Regulation
As the absence of contamination on the products used in the food sector is essential, there are very binding regulations that provide for the material and the process used to produce the components. The most important regulation is the one known in Italy as MOCA.
FCM translates as Food Contact Materials. These are materials and objects aimed at extending the shelf life – or at maintaining and improving the conditions – of packaged food. This regulation lists the materials that can come into contact with food, and also points out the methods of use and of production of the same elements. In particular, the regulation provides that all materials and products must be produced in compliance with good manufacturing practice and, under normal or foreseeable conditions of use, must not allow components to transfer to food in quantities that may:
- constitute a human health hazard;
- result in an unacceptable change in the composition of the foodstuffs;
- bring about a deterioration of the organoleptic characteristics.

Production Technologies
There are mainly two types of dies that are produced in the cold stamping of sheet metal for the food industry.
Progressive dies allow a product to be manufactured from a strip by means of successive deformations of the part. This type of product includes those that are trimmed and bent in large quantities. It would not make sense to make a progressive die for small quantities. As a matter of fact, the tool would turn out to be very expensive, and its cost would weigh significantly on each product. A progressive die, however, has a significant advantage for food applications: it minimises contact with the stamped parts, thus eliminating any danger of contamination. The raw material is unwound from the strip, which is fed directly into the die that is mounted on the press. Trimming and bending of the parts takes place automatically, without needing to touch the components. This mode, apart from the use of oils for lubrication during the stamping process, results in an uncontaminated product. There are special lubricants that evaporate after stamping, thus leaving the component clean. It is important to check, when defining the product characteristics, what type of lubricant can be used in the press. Mechanical presses are normally used with this type of die. They guarantee higher productivity as they offer a higher number of strokes per minute. Caps, brackets, and small containers are typical applications for this type of tools and sheet metal stamping, regardless of the material used.
- DEEP-DRAWING DIES
In order to manufacture wide, curved parts or food containers, such as steel or aluminium trays, deep drawing dies are the most commonly used. Their production technology is more complex and, especially for stainless steel deep drawing, there are important constraints that must be considered to manufacture products within the appropriate dimensional tolerance, without any wrinkles and any other surface imperfections. Usually, by deep drawing we mean the process whereby a material is stretched during the forming process. The advantage of using deep drawing for products for the food industry results from what may apparently seem to be a technological limitation. In fact, cold deep drawing of sheet metal requires that the geometry of the part to be produced does not have any 90° angles. This means that the shapes must be softened and have large radii of bending: the deeper the cold deep-drawn part, the larger the radii of connection of the surfaces must be.
In the production of deep-drawn parts for the food industry (such as trays and containers), this feature is extremely important, as it removes corners where dirt can lodge.
A rounded cold deep-drawn part makes cleaning easier. This allows cost-saving, since cold stamping is much cheaper than a welded product, and also proves to be a real advantage when using the part.
HOW WE CREATE VALUE
When developing products for the food industry, we are able to meet our customer’s specific requirements.
SIMULATIONS
We can carry out simulations to tackle the process effectively, thus making it robust when stamping.
This step allows us to agree with the customer on any changes to the component prior to the die design.
OPTICAL SCANNER
F.lli Poli are also the proud owners of a state-of-the-art optical scanner.
This device allows us to check the correct dimensions and shapes of any product after both progressive and deep-drawing stamping.
By detecting the dimensions of the product on both sides and combining the scans, we can check the thickness of the part, point by point, without having to section the part (therefore by means of a non-destructive test).
This allows to check the consistency of the technical features of the stamped part when particularly important safety requirements are needed.
USING 3D LASER CUTTING
In deep drawing, we have the advantage of having a laser for 3D cutting, so that the development of a trimming die is not needed.
This allows our customer to contain investment. Often, when new products are placed on the market, sales are uncertain, especially in the early stages of placement.
Deep-drawing requires not only the deep-drawing die needed to form the product, but also the trimming die that allows to trim the product once it has been deep-drawn. The cost of the trimming die is certainly as significant as the one of the deep-drawing die (especially for parts with a large trimming perimeter).
That’s exactly when the opportunity of 3D laser cutting offered by F.lli Poli is particularly advantageous.
We can carry out 3D laser trimming as it is possible to follow even very complex three-dimensional cutting paths, which allows to postpone investing in the trimming die until the market actually confirms its interest in the product.
PROTOTYPE PRODUCTION
Not only does this technology allow us to reduce investment costs, but it also enables us to create the first prototypes much faster than it would take to create them after manufacturing two dies.
Cutting masks for positioning the part on the 3D Laser equipment are still needed to be produced, but they are cheaper and faster to create than the trimming die.
Some of F.lli Poli’s applications
Our extensive experience in stamping for the food industry is the result of all the applications we have been developing over the years, focussing in particular on stainless steel stamping and aluminium stamping. Among other applications, we would like to mention:
An example of excellence
We are collaborating with a start-up that has brought a very interesting product onto the market: Cicara®. It is a product that revolutionises the way people have their coffee. The primary objective is to eliminate daily waste by saving thousands of plastic and paper cups.
Cicara® is made entirely of 100% recyclable materials.
The case and the lid are made of biodegradable bioplastic from renewable sources and based on corn starch. The tumbler is made of AISI 316 stainless steel, suitably treated after deep-drawing so as to be compatible with any food and drink. This application was very challenging indeed from a technical point of view. The product is made by using a progressive die designed and manufactured by F.lli Poli, who also deal with its stamping in their Fara Vicentino plant.
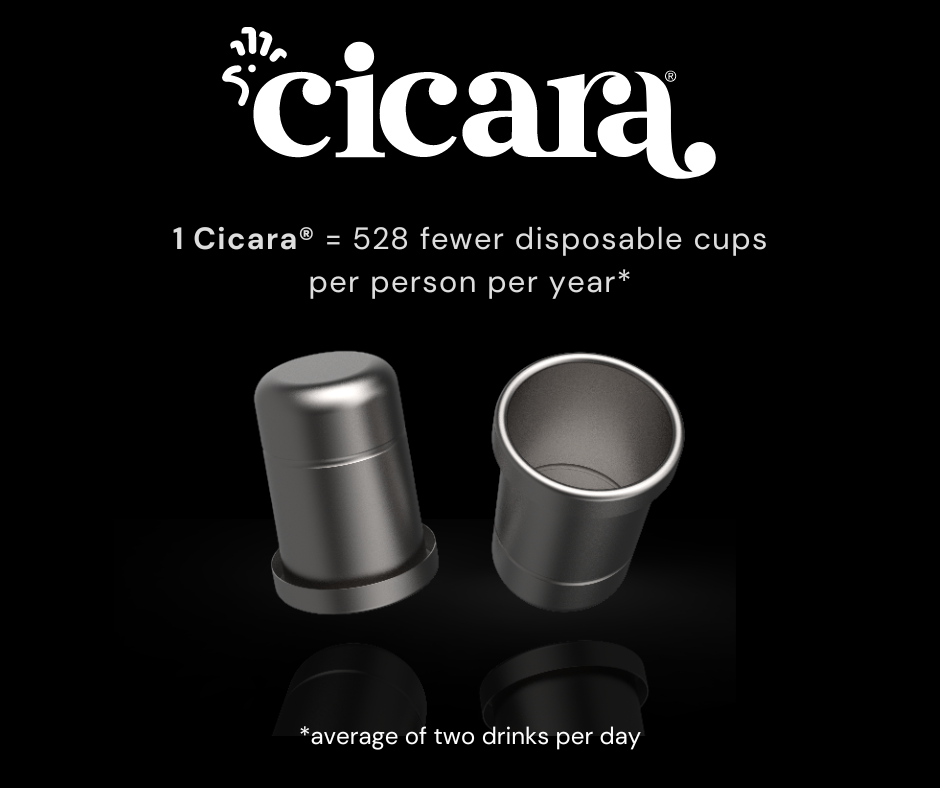
It is a very complex die going through eleven stages, six of which involve the deep-drawing process.
The need to create a flap on the rim of the tumbler to create the flare that comes into contact with the Cicara® user’s lips was quite a peculiar requirement.
The customer required that the tumbler had an aesthetically pleasing appearance for the user, therefore no aesthetic defect was allowed. Given the geometry of the part, marks were likely to appear on the flared rim due to the wrinkles resulting from the deep-drawing process. Special care was therefore taken while designing this part of the die.
The huge effort in its development has led to the creation of the die shown in the figure. It is a complex die that allows the component to be made from a strip of metal.
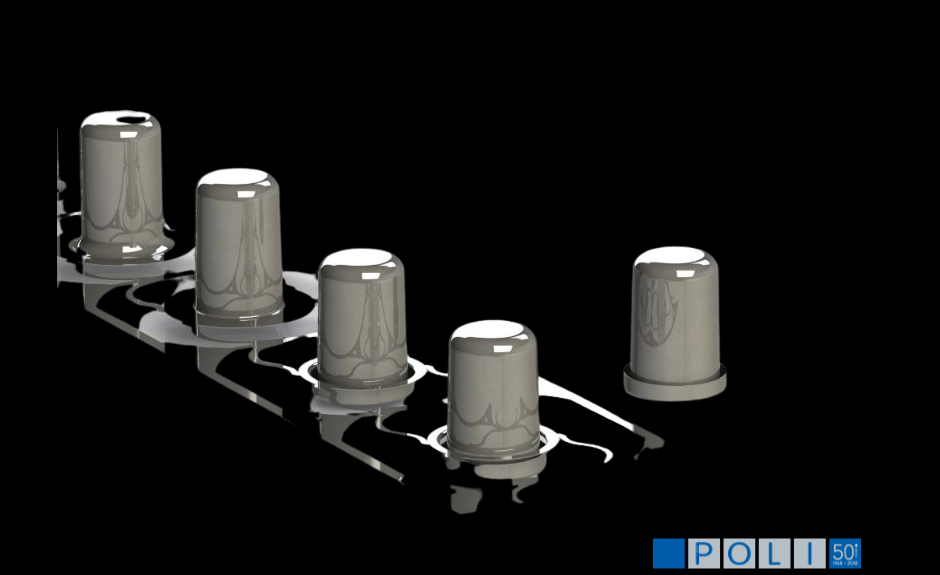
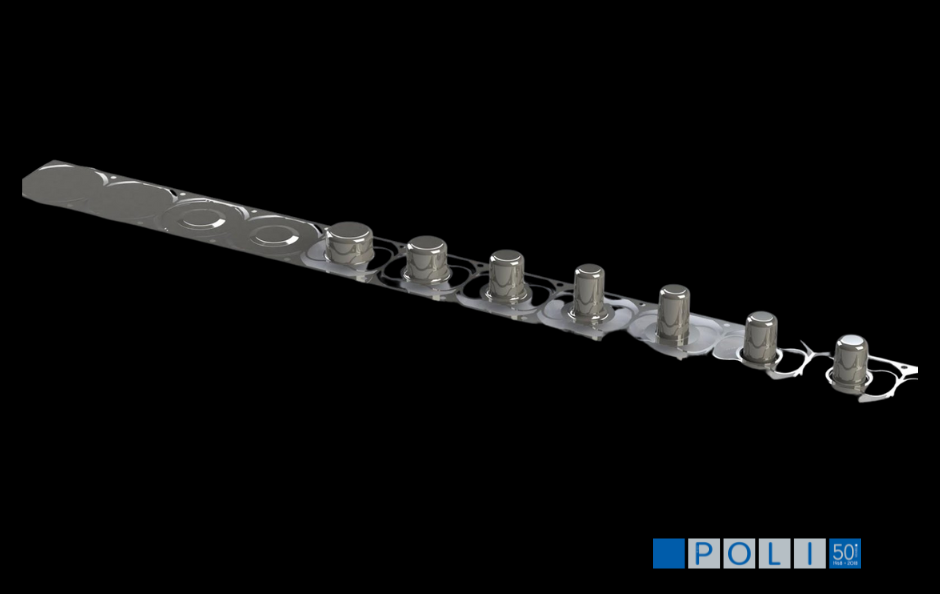
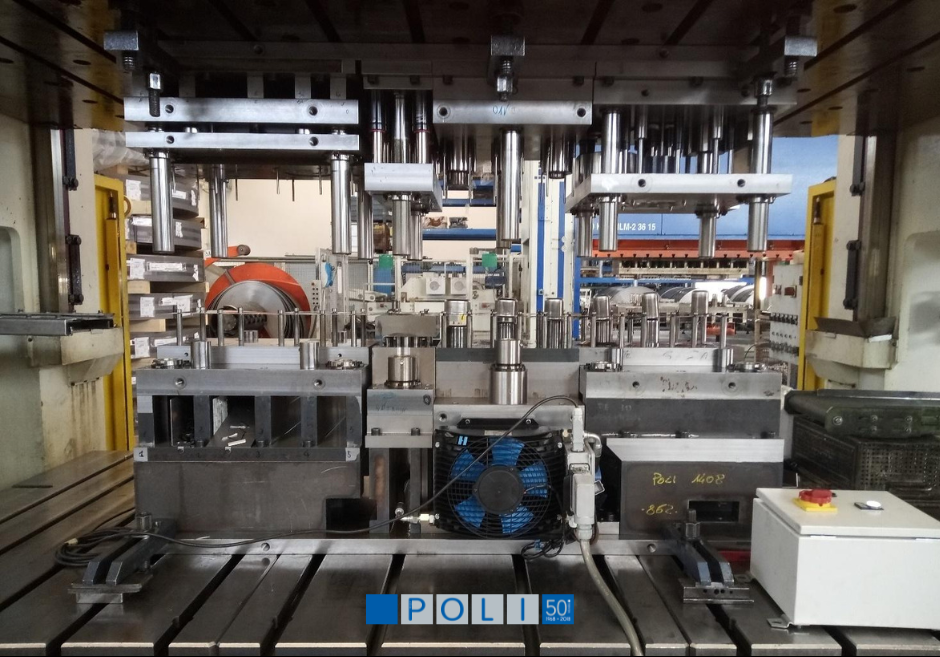
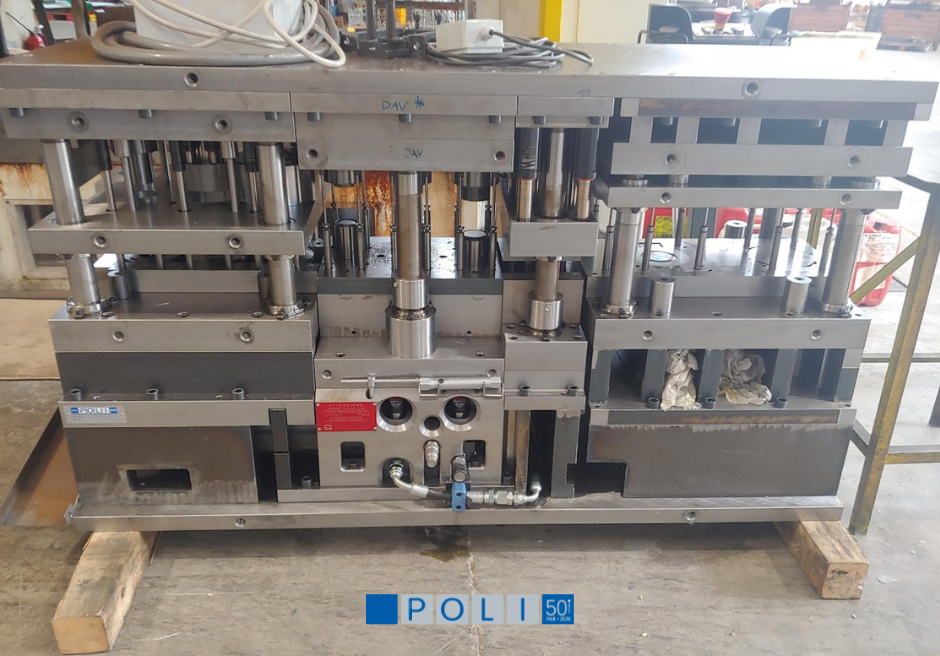